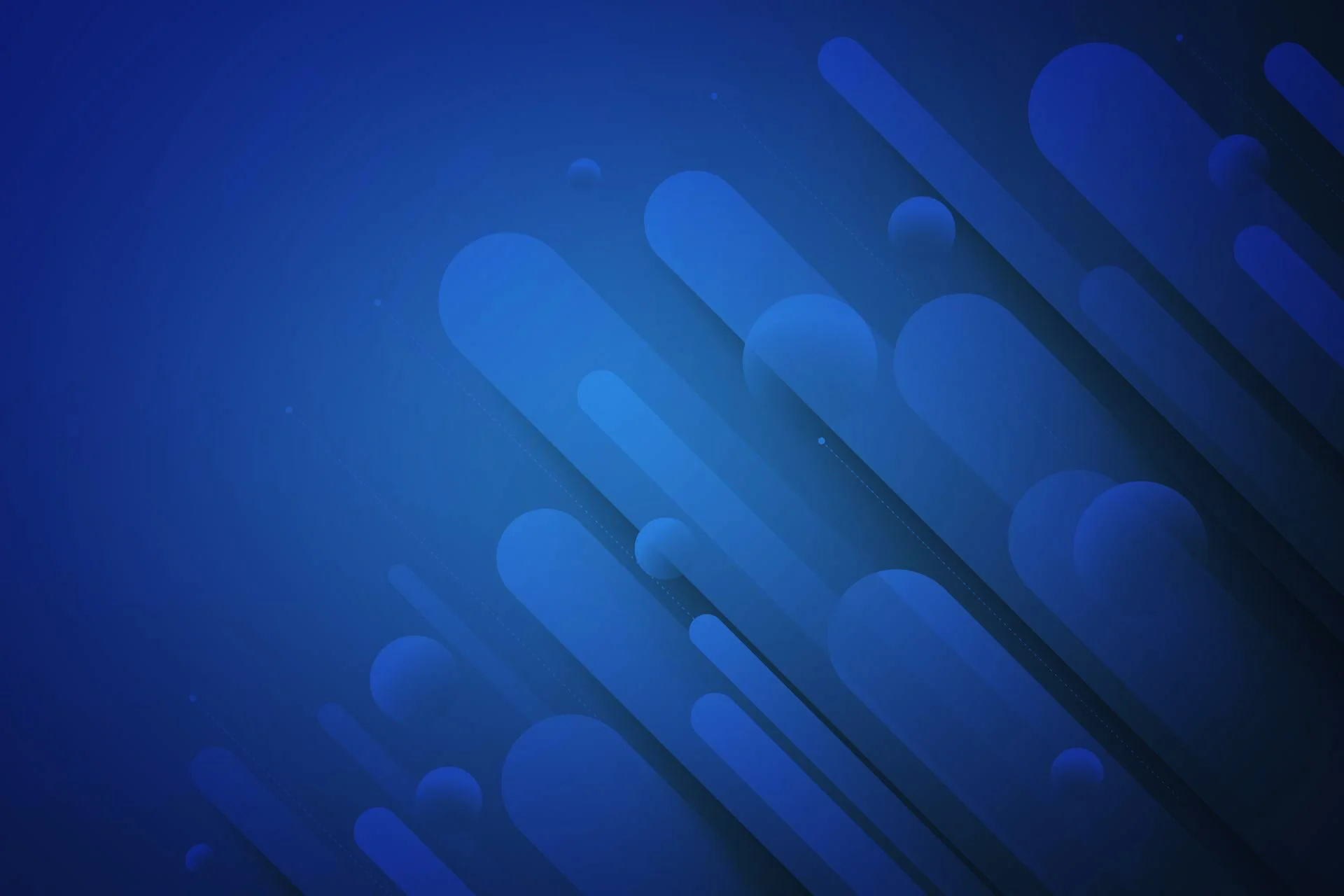
Kompetenzen
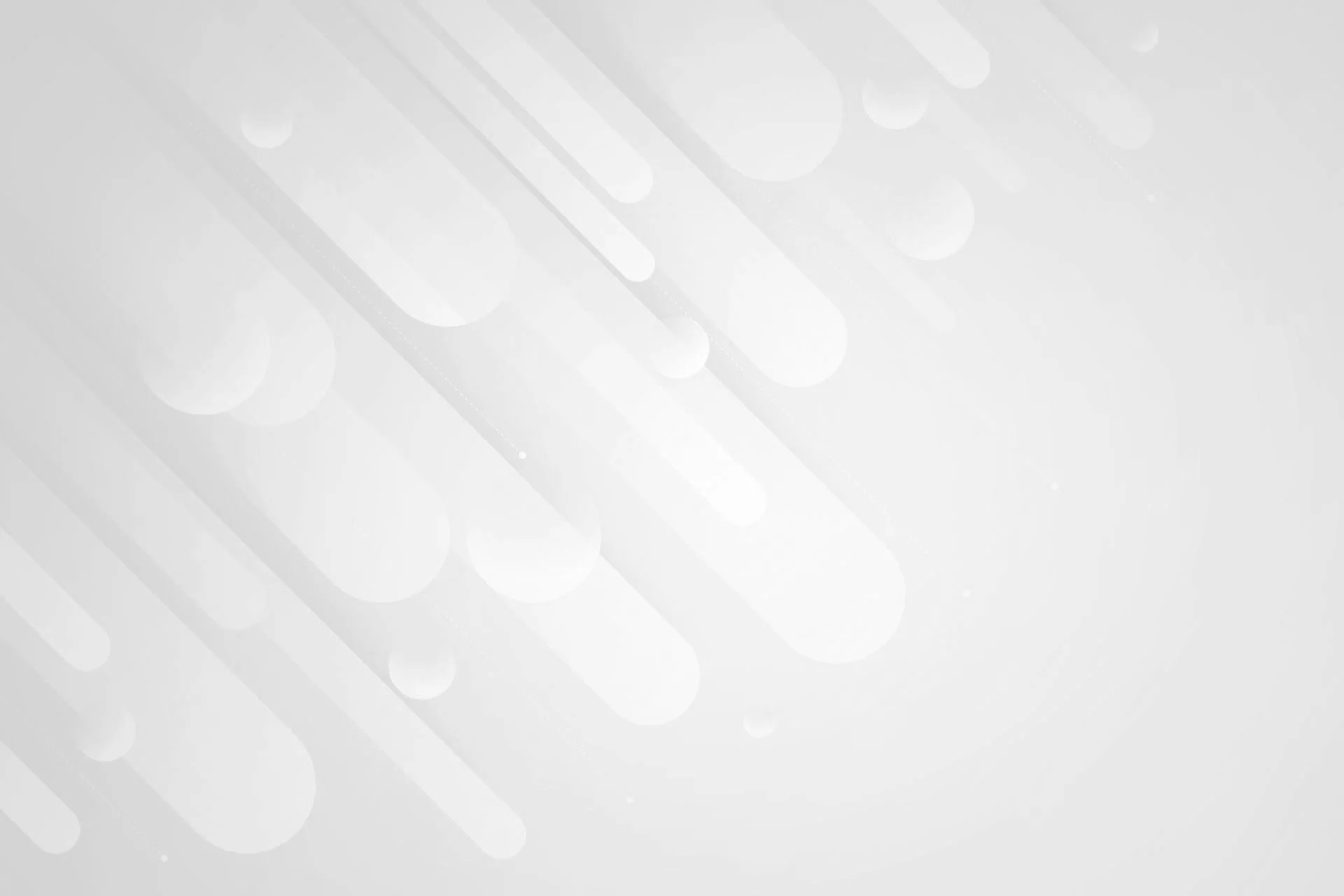
Lamellenfertigung
Seit Gründung unseres Unternehmens gehört die Lamellenfertigung zu unserer Kernkompetenzen
Wir haben diese Technologie so weit entwickelt, dass wir in der Lage sind auf mehreren Spuren simultan Lamellen herzustellen
Unsere Lamellen zeichnen sich durch maximale Flexibilität aus und sind variable in ihrer Form und Abmessung
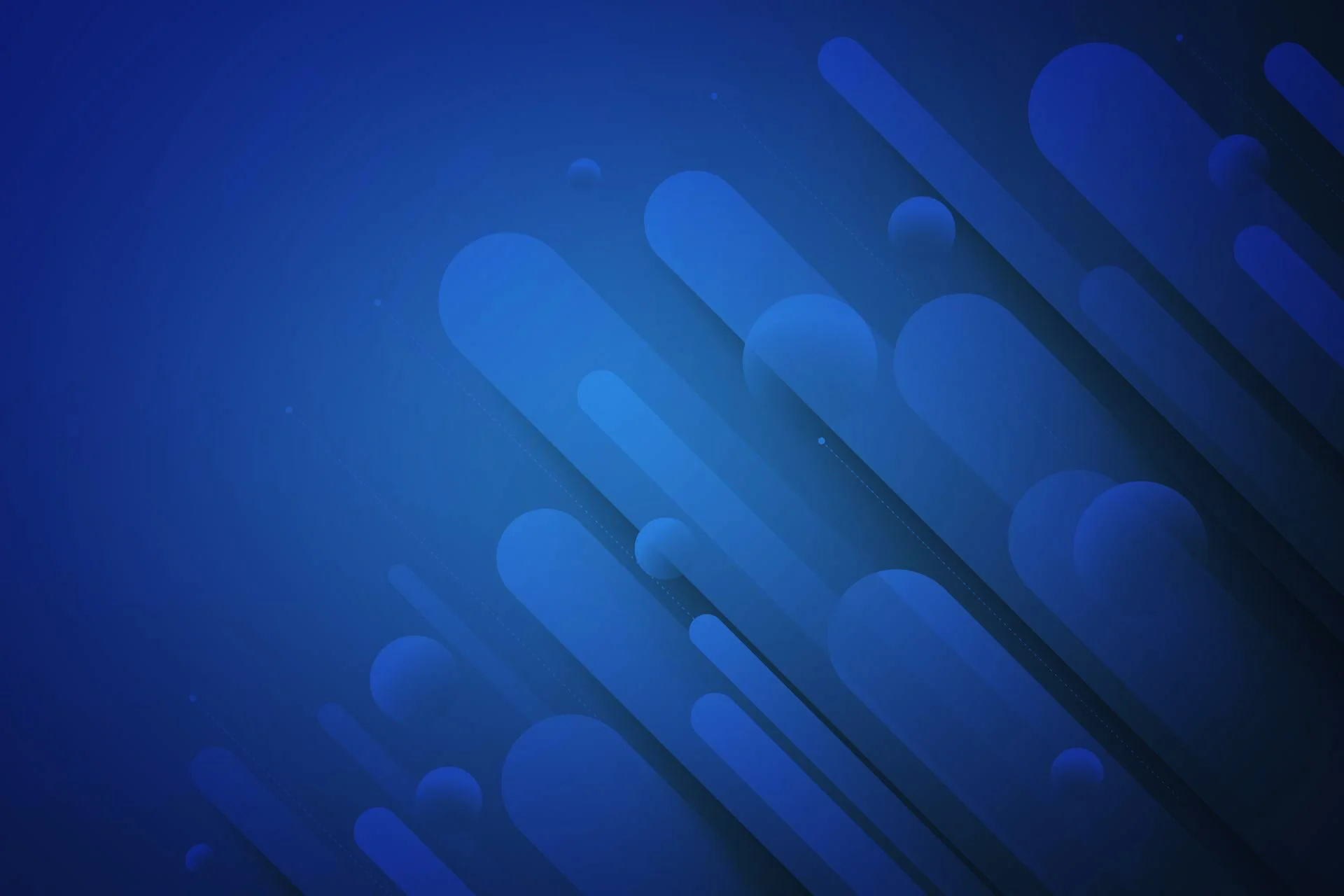
Faltrohrfertigung
Seit 2004 stellen wir verschiedene Arten von Aluminium-Faltrohr-Designs in Serienproduktion her
Eine temperaturkontrollierte Entfettung ist im Prozess enthalten und gewährleistet die für ein optimales Lötergebnis notwendige Reinheit
Eine kontinuierliche und kameraüberwachte Flussmittelbepastung gewährleistet eine optimale Rohrverlötung
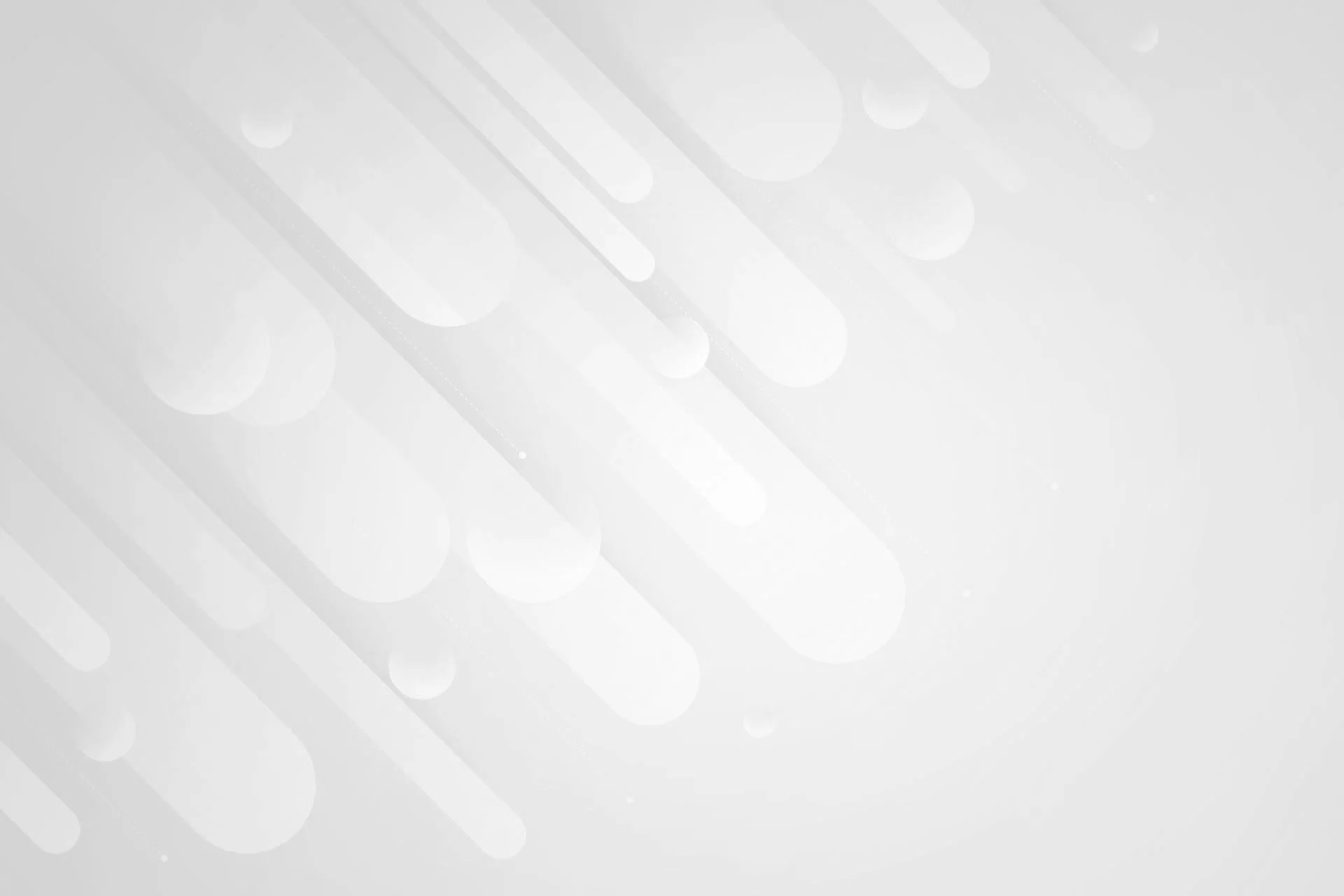
Fügen
Unsere Wärmeübertrager-Technologie ist eine höchst präzise und qualitativ anspruchsvolle Anwendung
Wir setzen verschiedene Fügesystematiken ein, um unsere Produkte zu fertigen
Bei der Anlagenbeschaffung achten wir besonders darauf, dass keine der Komponenten im späteren Herstellungsprozess beschädigt werden kann
Eine standardmäßige 100% Kontrolle der Fügeoperationen gewährleistet ein optimales Lötergebnis
Die besondere Herausforderung ist dabei Stanzteil-Komponenten so aufeinander abzustimmen und zu verbinden, dass höchste Qualitätsanforderungen erfüllt werden
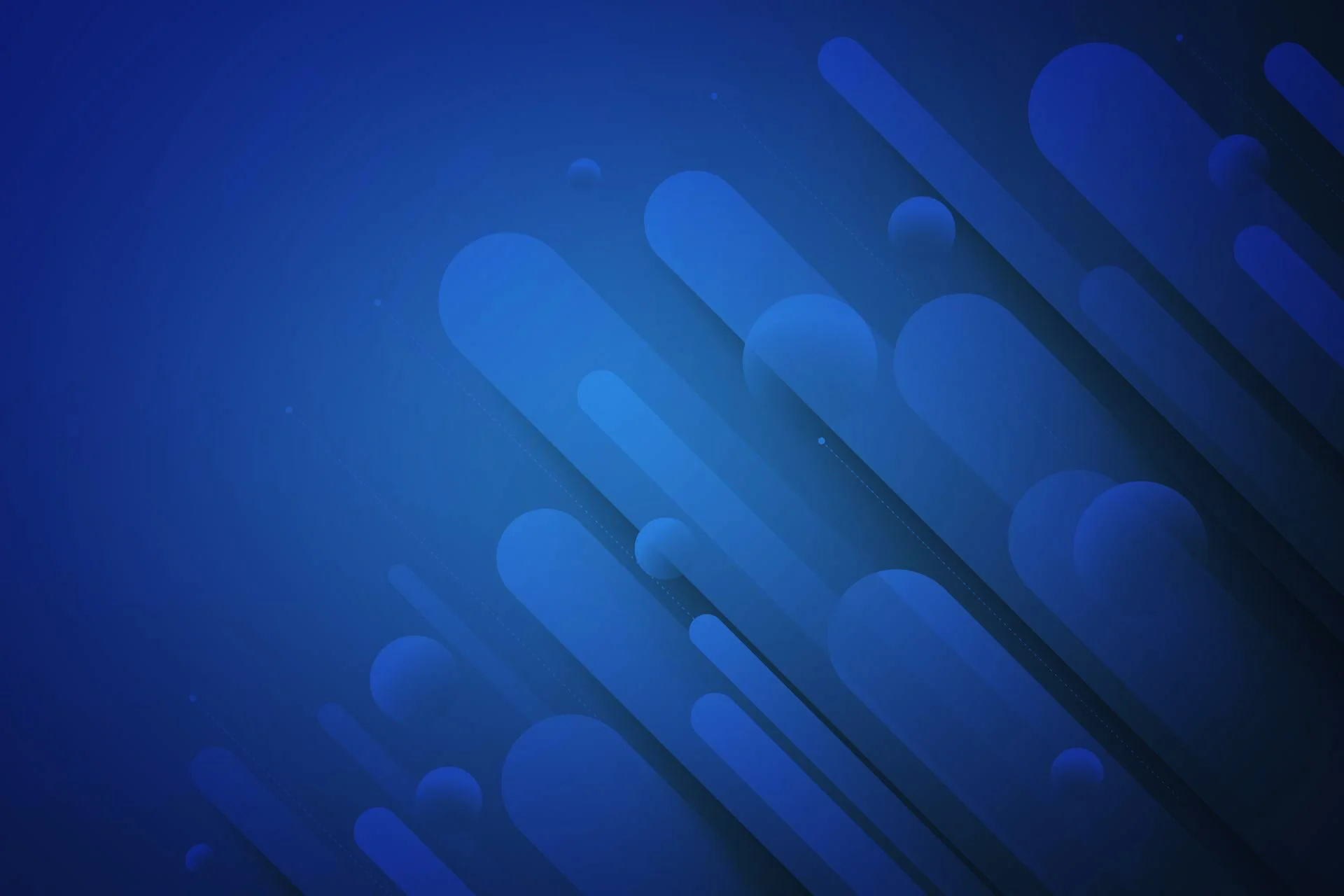
Schweißen
Um Stabilität bis in den Lötprozess zu gewährleisten, setzen wir zahlreiche Schweißverfahren ein
Unser Know-How umfasst WIG-Verfahren, CMT-Verfahren sowie Widerstandsschweißverfahren
Der Einsatz von verschiedensten, jeweils auf den Anwendungsfall abgestimmter Verfahren ermöglicht uns die Prozesssicherheit deutlich zu erhöhen und unsere Wertschöpfung nachhalttiger zu betreiben
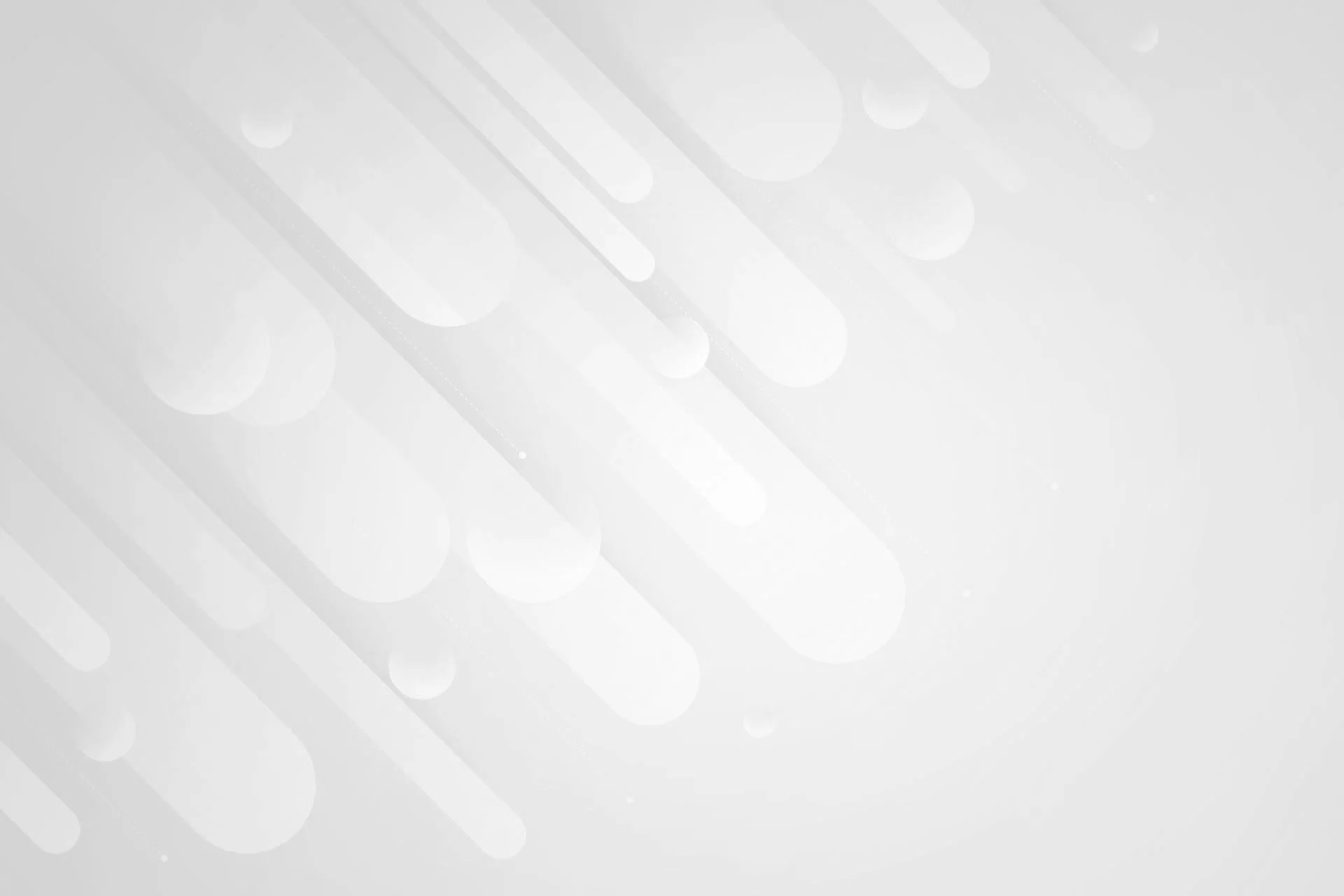
Lotpasten Applizierung
Gezieltes Auftragen der Lotpaste - punktgenau und mengenabgestimmt für beste Lötqualität
Komplexeste Konturen und Abfahren von Geometrien möglich
Verschwendung von Lotpaste dadurch vollständig vermieden
Hoher Automationsgrad und Eliminierung von manuellen Einflüssen durchgängig gegeben
Applikationsmengenüberwachung und 100% Rückverfolgbarkeit

Löten
Ein elementarer Kernprozess bilden unsere Vakuumöfen
Hochvakuum Lötprozess mit einem Temperaturrange von 1150°C - 1200°C Löttemperatur
Optimierte Programme zur Gewährleistung von hochwertigen Prozessabläufen
Löten ist ein höchst präziser und exakt abgestimmter Prozess, um ein robustes und langlebiges Produkt zu erzeugen
Neben Edelstahlapplikationen sind auch Kupferapplikation erfolgreich und prozesssicher lötbar
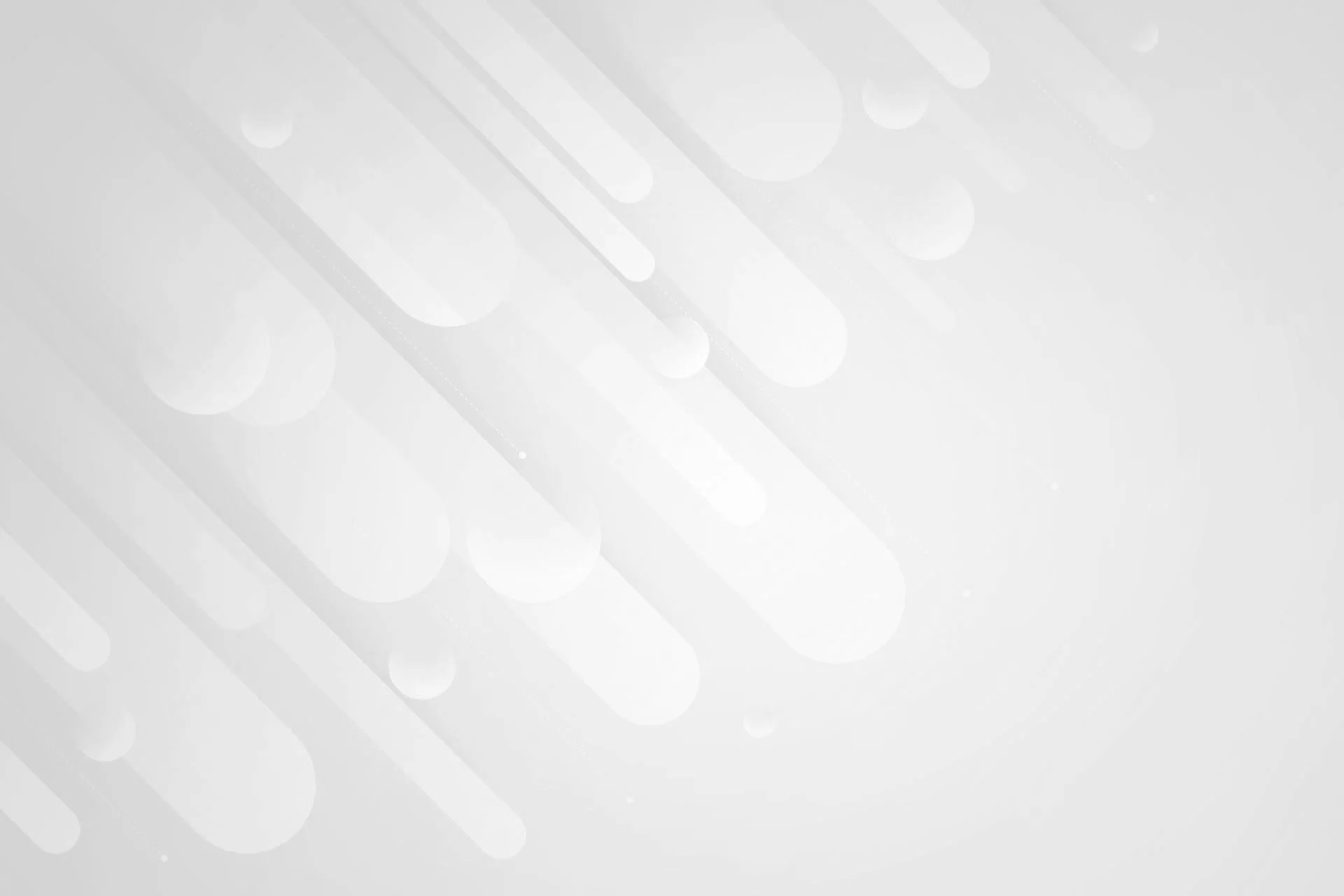
Aluminiumlötung
Unser kontinuierlicher Lötofen mit kontrollierter Atmosphäre (CAB) für Aluminium ist einer unserer Kernprozesse
Seit mehr als 25 Jahren löten wir Kühlnetze aller Größen sowohl in kleinen wie auch in sehr großen Stückzahlen
Unser Lötproduktportfolio umfasst luft- und flüssigkeitsgekühlte Ladeluftkühler, Kühlmittelkühler sowie Ölkühler und Batteriekühlplatten

Prüfen
Unsere End of Line (EOL) Anwendungen umfassen ein breites Spektrum an Anlagenlösungen, um die Kundenanforderungen sicherzustellen
Durch den aufgebrachten Data Matrix Code können wir eine durchgängige Rückverfolgbarkeit über den gesamten Prozess darstellen
Mit verschiedenen Systemen erhöhen wir die technische Sauberkeit unserer Endprodukte, um die hohen Reinheitsgradanforderungen der Automobilindustrie zu erfüllen
Eine 100% Leckageprüfung gehört zu unseren Standards im EOL Prozess, so dass der Kunde ohne weitere Prüfungen unsere Produkte direkt am Einsatzort verbauen kann
Des Weiteren setzen wir auf optische Kontrollen, um sicherzustellen dass die erforderlichen Komponenten in richtiger Anzahl auch an den jeweiligen Netzen verbaut wurden
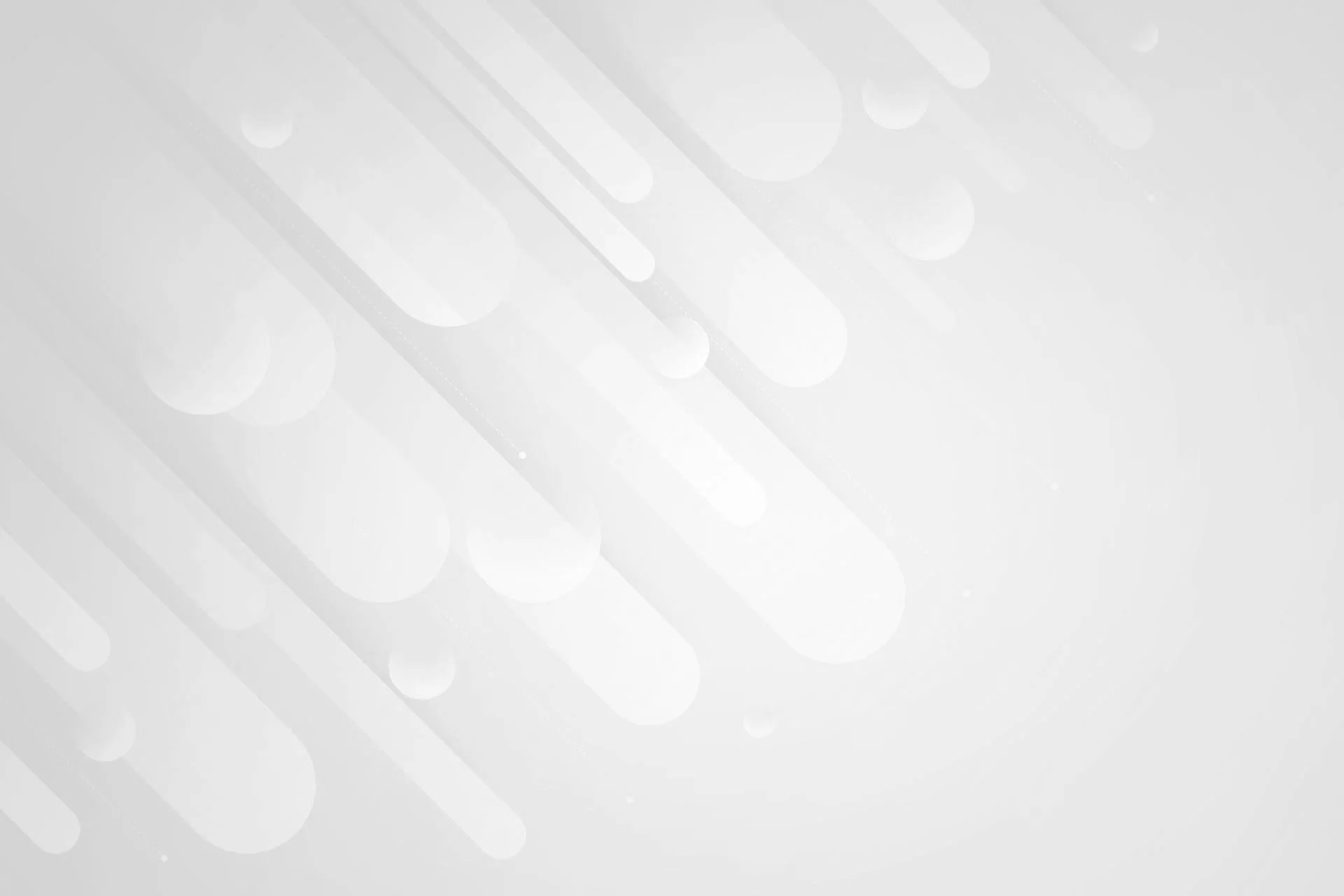
EOL – Montage, Vermessen, Prüfen, Einpacken
Drehwinkel, Drehmoment und Einschraubtiefen permanent überwacht und digital dokumentiert
100%-Prüfung aller funktionsrelevanten Maße zur Sicherstellung der problemlosen Montage am Kundenstandort
Dichtprüfung der kühlmittel- und gasführenden Medienkreisläufen und internen Schnittstellen
Visuelle Kontrolle von Merkmalen gemäß Grenzmusterkatalog
Verpackung in Kleinladungsträger mit VDA Kennzeichnung
Überwachung der Packungsdichte
Durchgängige Prozesskontrolle auf Vollständigkeit der vorgelagerten Prozesselemente